Preventive maintenance is defined as regularly scheduled inspections, tests, servicing, replacements, repairs and other tasks intended to help reduce the impact and frequency of equipment failures. This includes scheduled preventive maintenance, predictive maintenance and inspection activities.

The objectives of a preventive maintenance program are to help:
A preventive maintenance schedule is a scheduled maintenance or service check of an equipment. Preventive maintenance periodically checks an equipment to ensure that the equipment is operating properly and to avoid unscheduled breakdown of the machine, which causes downtime in business operation. Developing Your Preventive Maintenance Program. By Owe Forsberg. You are the new Reliability Engineer in a plant that currently lacks documented procedures to maintain the plant. You have been asked to develop preventive maintenance procedures (PM’s) for the plant and a target of 6 months to complete the project.
- Identify maintenance actions on important equipment and incorporate that into the preventive maintenance program activities that result in the greatest benefit within the available budget.
- Minimize corrective and breakdown maintenance, maintain satisfactory equipment conditions and improve plant reliability
A preventive maintenance program should be well defined, periodically reviewed and adjusted as necessary. To help ensure proper implementation, procedures should be written in sufficient detail for each piece of equipment in the program.1
Why is preventive maintenance important? The purpose of preventive maintenance is to try to maintain the equipment in optimum working condition and to help prevent any unplanned downtime due to breakdowns. Because components start to wear over time, replacing items prior to failure can cost you far less than the potential consequences of failure while in service. Some people see maintenance as an expense and it can often be one of the first departments to suffer from cuts during difficult times, however, this is very much false. Preventing problems from occurring will almost always be far less than the costs you will incur due to actual failures.2
1https://www.myodesie.com/wiki/index/returnEntry/id/3010
2https://www.buildings.com/article-details/articleid/6835/title/preventive-maintenance-checklist
Preventive Maintenance Checklist
Use the list below as a guide to help ensure you are doing everything you can to maintain an efficient facility.
LIGHTING
- Inspect at regular intervals, with group relamping when lamps begin to fail.
- Any luminaires that have transformers, control gear or accessories, such as spread lenses, glare baffles or color filters, should be routinely checked.
- Check exterior lights to make sure cables aren’t torn; all screws and hardware should be in place and working. Gaskets can be replaced to help provide a better watertight seal.
- Replace any burned-out lamps and consider group relamping (to create your relamping schedule, calculate lamp life and how often lamps are used).
- Ensure that each lamp has the same color temperature.
- Re-aim adjustable lighting if necessary.
- Dust lamps and clean lens surfaces to enhance lighting performance.
- Check all exit lighting for proper installation and function.
- Check all interior lighting for proper installation and function.
- Check all exterior lighting for proper installation and function.
Source: http://www.buildings.com/article-details/articleid/6835/title/preventive-maintenance-checklist.aspx/
ELECTRICAL
- Change batteries in smoke and carbon monoxide detectors, flashlights and test instruments.
- Confirm that timers and photocells are functioning correctly.
- Inspect cover plates for cracks and proper tightness.
- Inspect and clean all exhaust fans.
Source: http://ecmweb.com/content/preventive-maintenance-motors-and-controls
SAFETY
- Check inventory and restock all first aid kits.
- Check eyewash bottles and stations.
- Ensure safety signs and equipment labels are in good condition.
- Inspect and clean respirators.
- Inspect fall protection harnesses and kits.
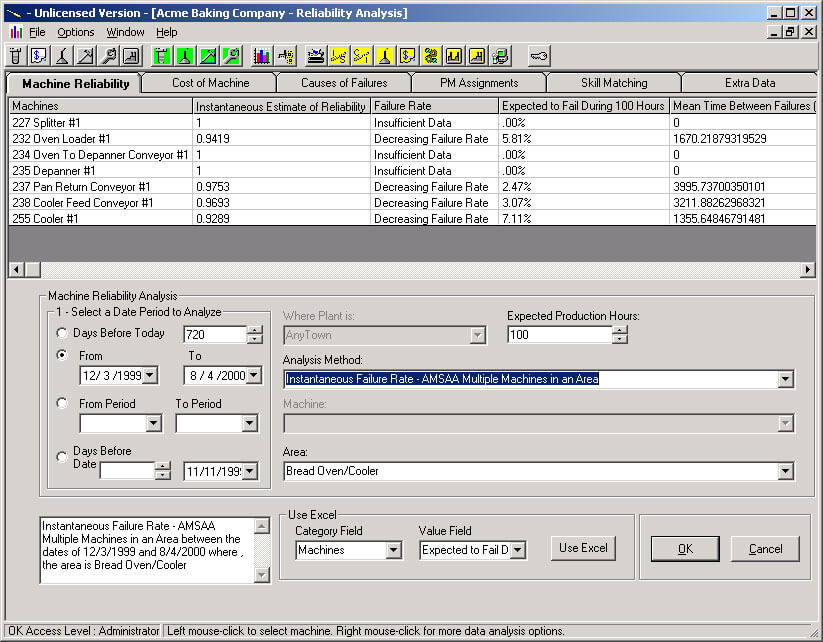
HVAC/R and PNEUMATICS
- Clean the air intake as needed.
- Change all air filters as needed.
- Check blower motors in operation for excessive noise or vibration.
- Clean motors and ductwork as needed.
- Check the condensate drain pan for proper drainage.
- Check the flexible duct connectors.
- Secure any loose guards and panels.
- Inspect the condition of all electrical hardware and connections.
- Test the safety controls and equipment.
- Check for proper operation of the interior unit.
- During the cooling season,
- Inspect the condenser motor bearings for excessive noise or vibration.
- Inspect the condenser air intake, discharge and coil as required.
- Check the condition of all refrigerant piping and insulation.
- Secure any loose guards or access panels.
- Check the operation of the exterior unit.
- Inspect compressed air lines regularly; investigate any leaks in piping, tubing or fittings.
- Replace or clean air filter elements at least quarterly, or as necessary depending on the application.
- Monitor oil levels on air compressor pumps and replace as necessary depending on usage.
- Inspect the condenser motor bearings for excessive noise or vibration.
Source: https://www.myodesie.com/wiki/index/returnEntry/id/3010
BUILDING INTERIOR
- Examine the condition of floors, ceilings and walls for evidence of deterioration.
- Check for visible signs of leaks.
- Inspect for hazards (electrical, mechanical, structural, physical, tripping, etc.).
- Check the condition and operation of toilets and showers.
- Test smoke and carbon monoxide detectors.
- Test the fire alarm system.
- Check the firefighting equipment.
- Check all doors for proper operation; ensure that exits are not obstructed.
- Inspect the condition of door locks and closures.
- Ensure work areas and walkways are properly marked.
- Check for accumulation of trash in storage areas.
- Check for evidence of insect infestation.
- Inspect wear on cart casters and that shelving is properly labeled, organized and secure.

Source: https://www.myodesie.com/wiki/index/returnEntry/id/3010
BUILDING EXTERIOR
- Examine the condition of the paint and walls.
- Check for broken windows and doors.
- Examine the condition of all railings.
- Check for plants growing on the building or its foundation.
- Clean the roof as needed. Use care when working in high places; employ adequate fall protection.
- Clean roof drains and gutters as needed. Test drains and downspouts by flushing them with water.
- Inspect the condition of the roof.
- Inspect gutters for adequate anchoring and tighten if necessary.
- Inspect the stack and all roof penetrations.
- Remove any plant life growing on the roof.
- Clean up any debris found.
- Check the grounds for broken glass and debris.
- Examine the condition of the sidewalk.
- Examine the condition of the driveway and parking area.
- Check the storm water drains.
- Check the condition of plants and lawns.
- Examine the condition of trees; verify that no branches are about to fall.
- Check for cleanliness around the dumpsters.
- Examine the condition of any fencing.
Source: https://www.myodesie.com/wiki/index/returnEntry/id/3010
PLUMBING
- Inspect plumbing at least annually; investigate any leaks or unusual noises.
- Domestic water booster and circulation pump systems require bearing lubrication at least annually; inspect couplings and check for any leaks.
- Domestic water heaters and boilers should be fire-tested periodically, using flue-gas analysis to adjust the flue draft and combustion air input to help optimize efficiency.
- Remote drinking water chillers need condenser fan motor bearings lubricated annually. Check all contacts for wear and pitting, and run system control tests. Pump down the system and remove the refrigerant according to manufacturer instructions. Drain and replace oil in the compressor oil reservoir, including filters, strainers and traps.
- Sump and sewage ejection pumps are replaced on an as-needed basis, but should be checked for function. Exposed pumps should be lubricated annually.
Source: http://www.buildings.com/article-details/articleid/6835/title/preventive-maintenance-checklist.aspx/
Program For Preventive Maintenance Services
A well-executed preventative maintenance schedule results in reduced breakdowns and cost savings. Many organizations--with noble intentions--develop or hire-out preventative maintenance programs and schedules, only to file them away within a few months. Like any tool, the tool itself is worthless unless properly utilized in the right way.
A preventative maintenance—or PM—schedule begins to formulate once a few gaps in information are filled. Timing, as well as the tasks, is crucial for carrying out an effective PM plan. In order to determine the timing and tasks, the following information is necessary.
Create a register of all assets such as buildings, vehicles and equipment. Group the list in systems and subsystems. For example, list each structure or building individually. Next, list the associated systems that are common to all the buildings. Examples of included systems are air conditioners, lighting systems, plumbing and communication systems. Subsystems, or individual components, might include individual air conditioners, specific lighting panels, certain boilers, and the like.
Prioritize assets by degree of importance or criticality. Equipment or system failures that would directly affect safety, operational performance, or comfort and convenience, will rank accordingly. Systems affecting safety of personnel are the highest priority. The plan should be created for these systems first--before moving on to less critical equipment.
Perform life cycle and replacement cost analysis on all assets based on their priority. The life cycle cost includes the initial purchase, labor and parts, expended toward the asset over its entire useful life. Forecasting future costs is possible based on historical cost and the asset’s rate of deterioration. Replacement cost of each asset is essential in determining the amount of time and money to invest toward its preventative maintenance. For example, a $20 dollar telephone is not worth a $30 dollar per hour electrician to inspect or repair.
Engage the entire staff in the development of the preventative maintenance schedule as early as possible. Allow the technicians and staff—those who execute the schedule—to be involved in its development. This conveys a sense of ownership and creates stakeholders whom now have an interest in the PM plan and schedule succeeding.
Preventive Maintenance Program For Trucks
Constantly monitor asset performance once the schedule is put into practice. Tracking the number of breakdowns—and what broke—will help analyze the schedules effectiveness. After a few months, scheduling adjustments are needed based on current asset performance trends. Some task intervals will be extended, while others will be shortened. Continuously monitoring and correcting the PM schedule ultimately results in a best-in-class PM program.
Start with equipment manufacturer recommendations for preventative maintenance as a minimum.
Assign numbers to all assets included in the PM schedule for improved tracking purposes.
Preventive Maintenance Spreadsheet Template
- Schlegelfotos/iStock/Getty Images